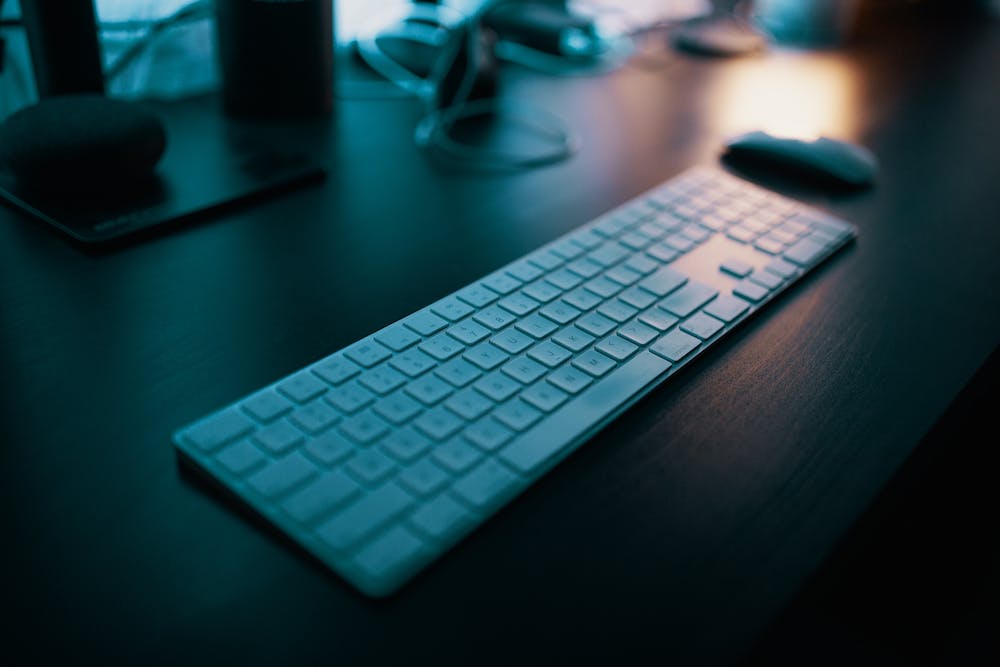
The Basics of Inventory Management: A Comprehensive Guide
Introduction
Inventory management is a crucial aspect of running a successful business. Whether you have a small online store or a large retail chain, effectively managing your inventory can help you streamline operations, reduce costs, and improve customer satisfaction. In this comprehensive guide, we will delve into the basics of inventory management, highlighting key principles, best practices, and strategies to help you optimize your inventory control.
Why is Inventory Management Important?
Inventory management plays a vital role in ensuring the smooth functioning of your business. Here are a few reasons why IT is crucial to prioritize effective inventory management:
1. Avoiding stockouts and oversupply
Accurate inventory management enables you to maintain optimal stock levels. By tracking sales data and forecasting demand, you can prevent stockouts that lead to lost sales opportunities. Similarly, avoiding oversupply helps avoid tying up capital in excess inventory.
2. Reducing carrying costs
Inventory carrying costs include warehousing fees, insurance, depreciation, and costs associated with obsolescence or spoilage. By optimizing your inventory levels, you can minimize these carrying costs and allocate resources more efficiently.
3. Improving cash flow
Efficient inventory management helps improve cash flow by reducing tied-up capital. By avoiding excessive stock levels, you can free up resources for other business investments or overhead expenses.
4. Enhancing customer satisfaction
A well-managed inventory ensures that customers can find the products they need when they need them. This leads to better customer satisfaction, repeat purchases, and positive word-of-mouth recommendations.
Key Principles of Inventory Management
To effectively manage your inventory, IT is essential to understand and implement these key principles:
1. Accurate record-keeping
Maintaining accurate records of your inventory is fundamental. Implementing a reliable system to track stock levels, sales, and incoming shipments helps in making informed decisions and preventing inventory discrepancies.
2. ABC analysis
ABC analysis categorizes inventory items into three groups based on their value and importance. Group A consists of high-value items that contribute significantly to revenue, Group B includes medium-value items, and Group C consists of low-value items. By applying this analysis, you can prioritize your inventory management efforts and allocate resources accordingly.
3. Just-in-time (JIT) inventory method
JIT is an inventory management technique where inventory is received from suppliers only when IT is needed to fulfill customer orders. This method helps minimize holding costs and reduces the risk of excess inventory.
4. Economic Order Quantity (EOQ)
EOQ helps determine the optimal order quantity that minimizes the combination of ordering costs and carrying costs. By calculating the right order quantity, you can optimize inventory holdings and reduce unnecessary expenses.
5. Safety stock
Safety stock is the additional inventory kept as a buffer to cover unexpected demand fluctuations or delays in supply. IT provides a safety net against stockouts and ensures uninterrupted order fulfillment.
Best Practices for Inventory Management
Implementing the following best practices can significantly improve your inventory management processes:
1. Regular inventory audits
Conducting periodic physical inventory counts alongside your stock records helps identify discrepancies, minimize shrinkage, and maintain inventory accuracy.
2. Utilizing technology
Leverage inventory management software or an enterprise resource planning (ERP) system to automate and streamline inventory-related tasks. These tools provide real-time visibility into stock levels, facilitate order management, and support data-driven decision-making.
3. Establishing effective supplier relationships
Building strong relationships with suppliers can lead to better pricing, reliable delivery schedules, and improved overall supply chain management. Collaborating closely with your suppliers enables you to maintain accurate demand forecasting and ensures a steady flow of inventory.
4. Implementing demand forecasting
Using historical sales data and market trends, develop demand forecasts to anticipate customer demand accurately. This helps you adjust inventory levels, plan for promotions or seasonal variations, and optimize order quantities.
5. Regular review of product performance
Analyze sales data to identify slow-moving or obsolete products and take appropriate actions such as liquidation, promotions, or discontinuation. This enables you to optimize inventory turnover and prevent excess stock buildup.
Conclusion
Efficient inventory management is essential to the success of any business. By adopting the principles and best practices discussed in this guide, you can streamline operations, reduce costs, and enhance customer satisfaction. Remember to regularly review and update your inventory management strategies as your business grows and industry dynamics change.
FAQs
Q: How often should I conduct inventory counts?
A: The frequency of inventory counts depends on the size and nature of your business. Small businesses may opt for monthly or quarterly counts, while larger businesses may conduct them more frequently, such as weekly or even daily.
Q: How can I prevent stockouts without tying up excessive capital in inventory?
A: Implementing demand forecasting techniques and utilizing inventory management software can help you strike a balance between preventing stockouts and avoiding excessive inventory levels. By accurately predicting demand and adjusting your order quantities accordingly, you can optimize your inventory while ensuring customers’ needs are met.
Q: What are the common challenges in inventory management?
A: Some common challenges include inventory inaccuracies, demand forecasting errors, supply chain disruptions, inventory spoilage or obsolescence, and maintaining optimal stock levels. However, with the right systems and strategies in place, these challenges can be effectively managed and overcome.