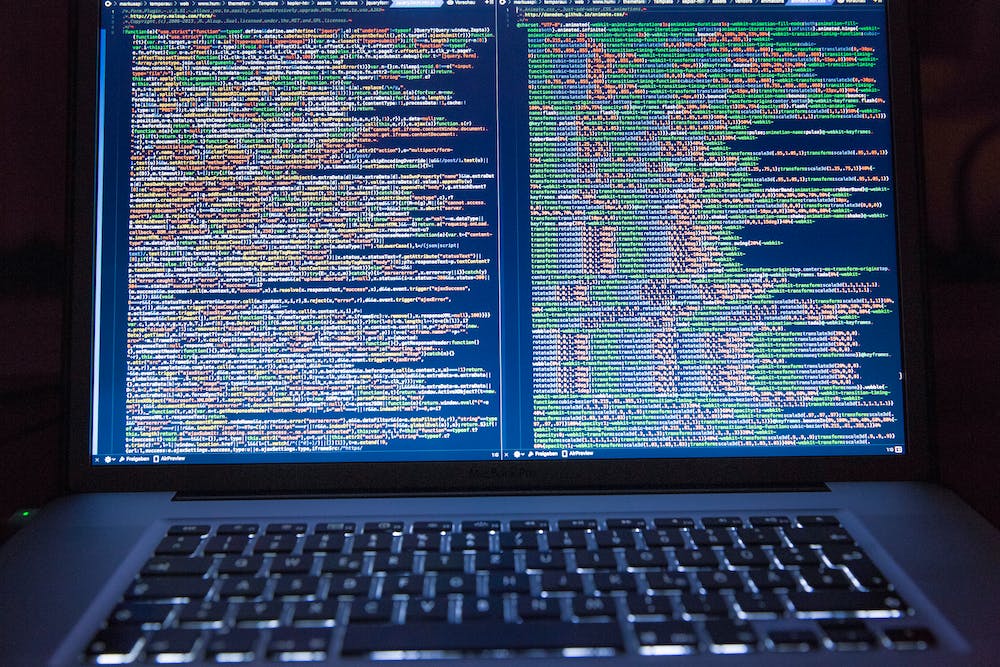
Exploring the Concept of Digital Twin in Manufacturing
Introduction
With rapid advancements in technology, the concept of digital twin has gained significant attention in the manufacturing industry. A digital twin is a virtual representation of a physical object or system, which provides a real-time and dynamic view of its performance and behavior. This article aims to explore the concept of digital twin in manufacturing, its benefits, and its potential applications.
Understanding Digital Twin
A digital twin is not simply a static 3D model or simulation. IT involves real-time data integration, analytics, and advanced visualization techniques to create a dynamic and interactive virtual representation of a physical asset or process. IT continuously receives data from sensors, machines, and other relevant sources, making IT a mirror image of its physical counterpart.
The integration of physical and digital worlds enables manufacturers to monitor, analyze, and optimize their operations remotely. By simulating different operational scenarios, manufacturers can identify potential issues, optimize performance, predict failures, and streamline processes.
Benefits of Digital Twin in Manufacturing
Implementing digital twin technology in manufacturing offers several advantages, including:
- Improved productivity and efficiency: Digital twins enable manufacturers to monitor and analyze their operations in real-time, leading to improved productivity and efficiency. By identifying potential bottlenecks or inefficiencies, manufacturers can take proactive measures to optimize processes and reduce downtime.
- Reduced costs: Digital twins help manufacturers identify areas where costs can be reduced. By closely monitoring performance and analyzing data, manufacturers can identify energy-saving opportunities, streamline maintenance, optimize supply chain operations, and reduce overall operational costs.
- Enhanced product development: Digital twins facilitate product development by allowing manufacturers to simulate different design variations and test their performance virtually. By iteratively improving and validating designs in the virtual realm, manufacturers can reduce the time and cost associated with physical prototyping.
- Better asset management: Digital twin technology enables manufacturers to monitor the health and performance of their assets in real-time. By analyzing data collected from sensors and other sources, manufacturers can predict and prevent failures, schedule maintenance activities, and extend the lifespan of their assets.
- Remote monitoring and control: With digital twins, manufacturers can remotely monitor and control their operations, even from a different location. This capability is valuable for companies with global operations or multiple manufacturing sites.
Applications of Digital Twin in Manufacturing
Digital twin technology has found applications across various sectors within the manufacturing industry. Some notable applications include:
- Smart factories: Digital twins are instrumental in the development and operation of smart factories. By creating a virtual replica of the production facility, manufacturers can optimize production processes, monitor equipment health, and implement predictive maintenance strategies.
- Supply chain optimization: Digital twins enable manufacturers to model and analyze their supply chain networks, identifying potential bottlenecks and optimizing logistics operations. This helps minimize inventory costs, streamline delivery processes, and enhance overall supply chain efficiency.
- Quality control: Digital twins allow manufacturers to simulate and test product quality and performance in a virtual environment. This helps identify potential defects or issues early on, enabling manufacturers to implement corrective measures and improve product quality.
- Operational maintenance and planning: Digital twins aid in the planning and execution of operational tasks, such as maintenance and facility management. By visualizing different maintenance scenarios, manufacturers can optimize maintenance schedules, reduce downtime, and improve overall operational efficiency.
- Worker training: Digital twins can be used for simulation-based training programs, allowing workers to gain hands-on experience in a virtual environment. This helps in skill development, reduces the risk of accidents, and enhances overall worker competency.
Conclusion
The concept of digital twin presents immense opportunities for the manufacturing industry. By integrating physical and digital worlds, manufacturers can optimize processes, reduce costs, improve product development, and enhance overall operational efficiency. The ability to remotely monitor and control operations and simulate different scenarios provides a competitive edge in an increasingly dynamic and demanding market.
FAQs about Digital Twin in Manufacturing
Q: What is a digital twin?
A: A digital twin is a virtual representation of a physical object or system that provides real-time and dynamic insights into its performance and behavior.
Q: What are the benefits of implementing digital twin technology in manufacturing?
A: Implementing digital twin technology in manufacturing offers benefits such as improved productivity and efficiency, reduced costs, enhanced product development, better asset management, and remote monitoring and control.
Q: What are some applications of digital twin in manufacturing?
A: Digital twin technology finds applications in various manufacturing sectors, including smart factories, supply chain optimization, quality control, operational maintenance and planning, and worker training.
Q: How does a digital twin help in enhancing product development?
A: Digital twins allow manufacturers to simulate and test different design variations virtually, reducing the time and cost associated with physical prototyping, thereby enhancing product development.
Q: Can digital twins aid in asset management and maintenance?
A: Yes, digital twins enable manufacturers to monitor the health and performance of their assets in real-time, predict and prevent failures, schedule maintenance activities, and extend asset lifespan.