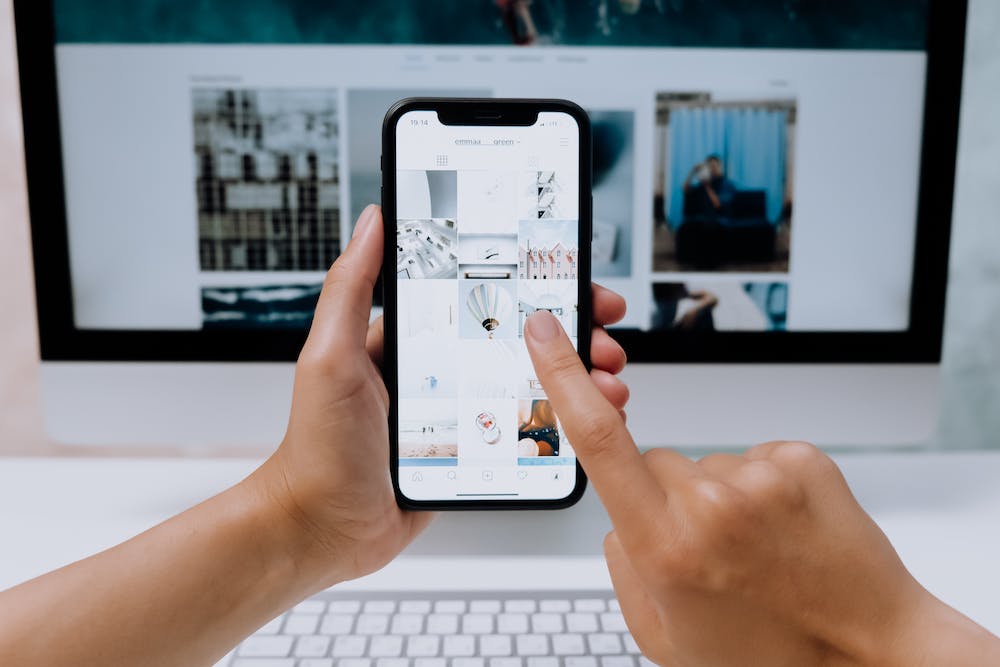
In today’s modern manufacturing environment, the integration of industrial information technology has become increasingly prevalent in factory automation. Industrial information technology refers to the use of advanced software, hardware, and communication technologies to automate and streamline the production processes in industrial settings. This article aims to explore the various benefits that industrial information technology brings to factory automation, and how IT enhances efficiency, productivity, and overall operational performance.
Increased Efficiency and Productivity
One of the primary benefits of incorporating industrial information technology in factory automation is the significant improvement in efficiency and productivity. Advanced technologies such as programmable logic controllers (PLCs), supervisory control and data acquisition (SCADA) systems, and industrial robots enable seamless coordination of various manufacturing processes. This results in optimized production workflows, reduced downtime, and increased throughput, ultimately leading to higher productivity levels.
Enhanced Quality Control and Monitoring
Industrial information technology also plays a crucial role in ensuring superior quality control and monitoring in factory automation. Through the implementation of real-time monitoring and data analysis tools, manufacturers can continuously track and analyze key performance indicators (KPIs), such as equipment performance, energy consumption, and product quality. This proactive approach to quality control allows for timely identification and resolution of potential issues, ultimately leading to higher-quality products and reduced waste.
Streamlined Maintenance and Predictive Asset Management
Another significant benefit of industrial information technology in factory automation is the ability to streamline maintenance processes and implement predictive asset management strategies. Through the use of advanced sensors and predictive maintenance software, manufacturers can monitor the condition of equipment in real time and predict potential failures before they occur. This proactive approach to maintenance not only minimizes unplanned downtime but also extends the lifespan of critical assets, resulting in significant cost savings and improved overall equipment effectiveness (OEE).
Flexible and Scalable Manufacturing Operations
Industrial information technology enables manufacturers to achieve greater flexibility and scalability in their production operations. With the use of advanced automation systems and intelligent control technologies, factories can easily adapt to changes in production requirements, such as product variations, batch sizes, and manufacturing processes. This level of flexibility allows manufacturers to respond swiftly to market demands and optimize their production processes, ultimately leading to increased competitiveness and customer satisfaction.
Improved Workplace Safety and Ergonomics
By integrating industrial information technology in factory automation, manufacturers can also enhance workplace safety and ergonomics for their employees. Advanced robotics and automated material handling systems minimize the need for manual labor in hazardous and physically demanding tasks, reducing the risk of workplace injuries and ergonomic-related issues. Furthermore, the use of predictive analytics and intelligent safety systems helps identify potential safety hazards and implement preventive measures, ensuring a safer working environment for all employees.
Conclusion
Overall, it is evident that industrial information technology plays a pivotal role in revolutionizing factory automation, offering a myriad of benefits that contribute to improved efficiency, productivity, and operational performance. By leveraging advanced software, hardware, and communication technologies, manufacturers can optimize their production processes, enhance quality control, streamline maintenance operations, and achieve greater flexibility and scalability. Moreover, the integration of industrial information technology also leads to improved workplace safety and ergonomics, creating a sustainable and conducive work environment for all employees. As the manufacturing industry continues to evolve, the adoption of industrial information technology will undoubtedly become increasingly indispensable for driving innovation and competitive advantage in factory automation.
FAQs
-
What is industrial information technology?
Industrial information technology refers to the use of advanced software, hardware, and communication technologies to automate and streamline production processes in industrial settings.
-
How does industrial information technology improve efficiency in factory automation?
By using technologies such as PLCs, SCADA systems, and industrial robots, industrial information technology enables seamless coordination of manufacturing processes, resulting in optimized production workflows and increased throughput.
-
What are the benefits of predictive asset management in factory automation?
Predictive asset management allows manufacturers to monitor the condition of equipment in real time and predict potential failures before they occur, resulting in minimized downtime and improved overall equipment effectiveness (OEE).
-
How does industrial information technology contribute to workplace safety?
By implementing advanced robotics and automated material handling systems, manufacturers can minimize the need for manual labor in hazardous tasks, reducing the risk of workplace injuries and ergonomic-related issues.